Piezo-Electric Vibratory Feeders Technology Overview
Sanki Drive Technology
Sanki Piezo-Electric drives use specially developed piezo elements to create very fine vibration. The vibration from the elements is amplified by carbon fiber springs, and the complete assembly of spring and element is mounted at the optimum angle to provide high feed speed with minimal vibration amplitude. This technology offers the following advantages:
- small or micro parts can be fed consistently without jams
- miniature feeders available to fit in compact spaces
- sensitive parts can be fed with minimal damage
- parts can be oriented based on very small features
- minimal magnetic field allows feeding of magnetically sensitive parts without resorting to false-bottom bowls
- low particulate emissions from system allows use in Class 10 (ISO 4) clean rooms without auxiliary enclosure
- Drives available in standard and low profile types, from 3″ to 18″ bowl diameter
- Drives run very quietly, typically eliminating the need for bulky and expensive sound enclosures
- Piezo elements are ideal for powering fully linear feed systems
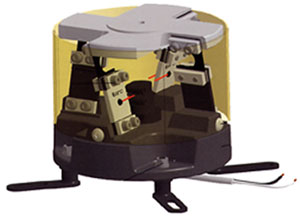
Call 905-763-9442 today to learn how
Sanki’s technology can work for you!
Check out some innovative feeding solutions powered by Sanki drives
Sanki Controller Technology
Sanki Piezo drives are controlled by fully digital variable frequency, variable voltage inverter controllers which include a display to show the exact frequency and voltage your system is running at. These controllers offer the following advantages over electro-magnetic vibratory controllers:
- Digital tuning – no spring adjustment necessary to setup or maintain your vibratory drive!
- 50/60 Hz auto correction – the controller will automatically filter out fluctuations in input frequency to maintain stable output frequency
- Displayed values for voltage and frequency allow optimum operating settings to be recorded for easy troubleshooting later
- Accelerometer feedback available to maintain rock-solid feed conditions even as heavy parts flow through the system
- Low cost compared to inverter controllers for electro-magnetic systems
- Very low power draw (70% less than some e-m systems)
- Frequency output up to 400Hz